
Motor Power (kW)
Motor Voltage
Mounting Type
Frame Size
Compact Frame
Material
Manufacturer
Quick View
Quick View
Quick View
Quick View
Quick View
Quick View
Quick View
Quick View
Quick View
Quick View
Quick View
Quick View
Quick View
Quick View
Quick View
Quick View
Quick View
Quick View
Quick View
Quick View
Quick View
Quick View
Quick View
Quick View
3 Phase Electric Motors
What is a 3 Phase Motor?
A 3 Phase Motor is an induction motor or asynchronous motor. In these motors, the electric current in the rotor is supplied by 3 separate phases, this then produces torque by means of electromagnetic induction from the stator winding. Induction motors are available in two types, the squirrel cage motor or the wound type.
At ACDC we supply the squirrel cage type motors due to their compatibility with Inverters and the compact size and reliability. Historically, these types of motors would have been used in a single-speed application, varying the number of poles to enable an element of speed control or selection, but with VFD's now becoming far more affordable and their cost savings becoming widely recognised, these motors are now used more and more in variable speed applications.
An estimated 30-40% of all newly installed asynchronous motors now include a VFD to control the speed or to offer enhanced functionality or cost savings on energy.
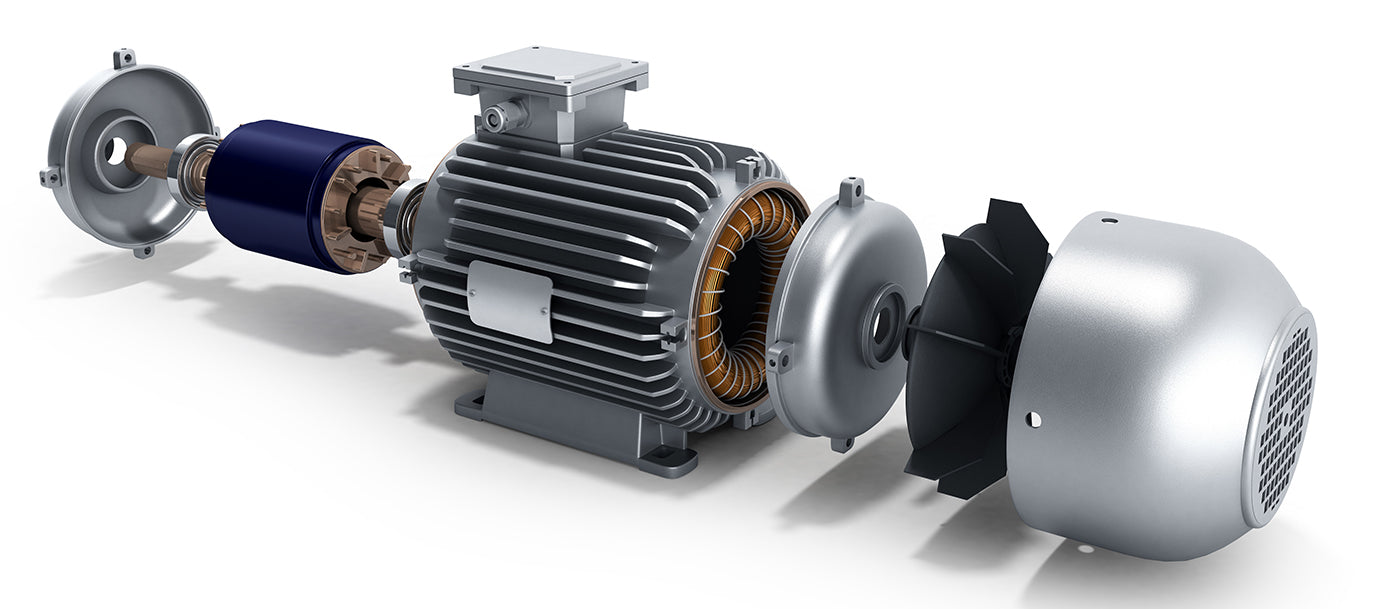
Aluminium or Cast Iron Framed Motor?
Aluminium 3 Phase Motors
Aluminium 3 Ph Motors offer a great compromise between weight and efficiency. They are perfectly suited to industrial use and in the smaller frame sizes are more frequently used than cast iron. An Aluminium frame motor will often weigh up to 30% less than its equivalent cast-iron motor although dimensionally the same. We offer Aluminium motors in 3 phase between 0.75kW and 37kW up to frame size 200.
Our Aluminium motors all feature sealed for life bearings. The fan and covers (cowls are independent and can be replaced if damaged or even swapped out for a Force Vent Unit if the motor will be used at low speeds for prolonged periods.
Our aluminium ranges feature Cast Feet, which can be bolted in different locations on the motor body to allow the motor in effect to be 'rotated', allowing for greater flexibility when mounting the motor. This also changes the position of the terminal box so it can be located on either side of the motor, again maybe saving space or making the location of the terminals easier to reach for servicing.
Aluminium motors due to the nature of the material also offer better resistance to corrosion in areas where the air or atmosphere is damp or contains corrosive particles.
Aluminium Motors can often be found in these applications:- Water Treatment / Sewage Plants
- HVAC Systems
- Food and Drink Manufacturing
- Conveyor systems
- Refrigeration
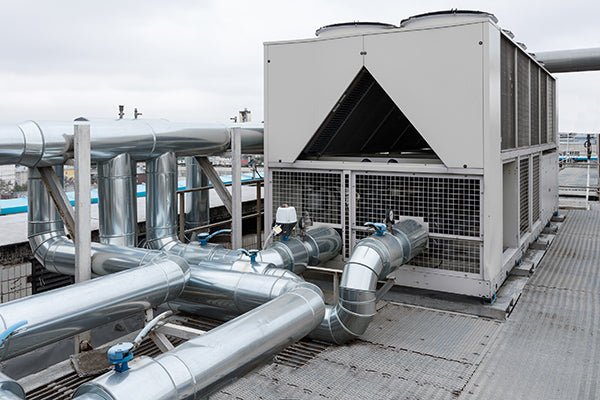
Cast Iron 3 Phase Motors
Cast Iron Motors are identical in size, but obviously, due to the nature of the material they are made from, weigh considerably more. Although this can be negative, there are a lot of beneficial aspects of this material; due to the material being stronger, the bearing seats will be better suited to larger loads, including side loads such as those exerted when using pulleys or belts, the cast iron also aids inductance, which is why the IE3 motors are usually only available with Cast iron frames.
Due to the costs of production, the prices of Cast iron start to become more competitive in the mid ranges of 11kW and above.
Our range of Cast Iron Motors are available from 0.75kW up to 355kW
Cast Iron 3Ph Motors can often be found in these applications:- Large Fans
- High powered pumps
- Scrap metal Plants
- Heavy Industry
- Extruders
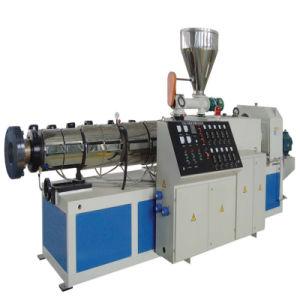
Motor Comparison
Aluminium 3 Phase Motors | Cast Iron 3 Phase Motors | |
kW Ratings | 0.75kW - 37kW | 0.75kW - 315kW |
Frame Sizes | 80 - 200 | 80 - 355 |
Suitable For Corrosive Environments | ||
Available in IE2 Efficiency | ||
Available in IE3 Efficiency | ||
Multi-Mount | Moveable Feet | Moveable Feet |
Frequency | 50 / 60 Hz | 50 / 60 Hz |
Can I Use 3 Phase Motors With An Inverter?
All motors in our range are inverter compatible and include the appropriate ratings on the name-plate on the side of the motor.
Slow Running For Prolonged Periods With An Inverter?
Please note that if the motor will be used to run at low speeds with an inverter for periods longer than a few seconds, the standard fan will not provide enough flow and you will require a Forced Vent Unit which will run off a separate supply and supply sufficient air to cool the motor.
This is due to the fact that a standard fan runs off the rotor and therefore operates at the same speed as the motor at any given time. If the motor is turning at 100rpm but under high load for example, then the fan will not be supplying enough airflow over the cooling fins to sufficiently cool the motor. The forced ventilation unit replaces the standard fan and is powered by a separate supply, maintaining airflow and cooling.
What Determines The Speed Of My Motor?
A motors base speed (or maximum RPM) is usually determined by the number of poles it has. The fewer the number of poles, the higher the maximum speed; inversely with more poles, the speed decreases, but the torque produced by the motor increases. The table below is a rough guide to the base speeds, these vary due to efficiency differences and are only nominal figures.
Number of Poles | |
2 Pole | 3000rpm |
4 Pole | 1500rpm |
6 Pole | 1000rpm |
8 Pole | 750rpm |
If the Output speed you require from your motor doesn't match the ones in the chart above, don't worry. By using either an Inverter or a Motor Gearbox, we can give you a solution for almost any speed you may require. By adding a gearbox, you will also significantly increase the final torque output from your motor. See our Gearbox section for more details.
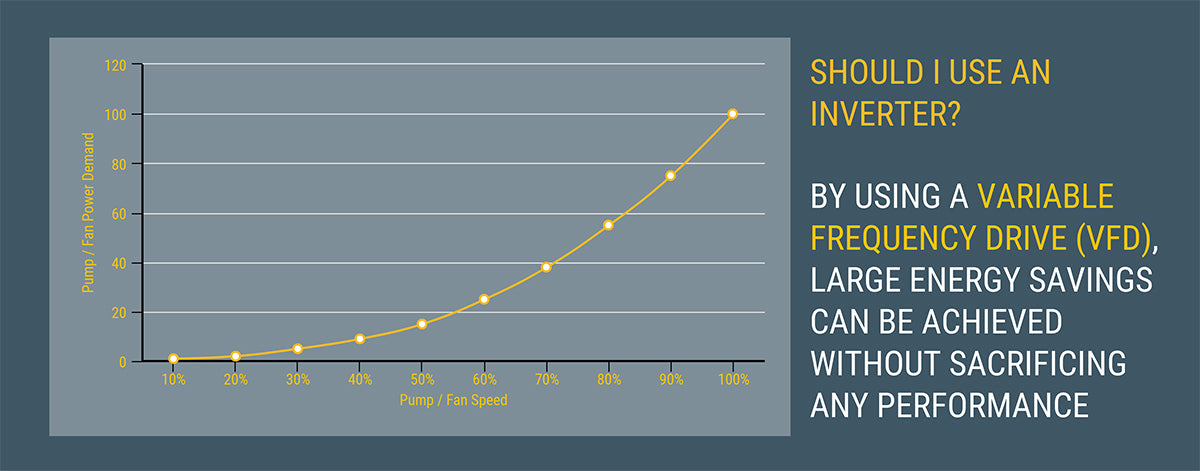
AC motor force ventilation
Can I fit a force vent to a standard motor? Yes, most manufactures of motors will supply a fan unit that will bolt on to the rear of the motors. Remove the old cowling and slip over the new unit making sure it is securely mechanically fastened.
Why do I need a cooling fan for my AC motor? When running the motor below the rated speed the impellor will not pass enough air over the surface of the motor and cause the motor to run hot. AC motors can be run to 0Hz and hold torque, when this is happens no cooling is present and so the motor will overheat. If the motor is set up in senseless vector or closed loop vector almost full torque is available down to zero speed.
As well as the 3 phase AC motor, can I run the force vent from the inverter? No, the fan will not operate correctly and will reduce in speed when the frequency is lowered at the very time you need cooling on the motor. Run an independent supply to the Fan making sure it is adequately protected with a thermal device i.e. an overload, Ensure that if it stops the overload is interlocked with the inverters run signal to prevent the motor running without cooling. Fans can be selected in either 1 phase or 3 phase variety, larger motors will have 3 phase option only.
What speed Can I run the motor to without cooling? This may vary depending on the manufacture and application however, this is generally below 35% - 50% of the motor speed, cooling is radically impaired due to the reduced impeller speed. Most motors today are inverter rated and come with thermistors installed as standard these should be installed into the control circuit or inverter to inhibit the operation if the temperature rise is above the normal operational temperature. Typically, the thermistor is around 250 Ohms and will increase in resistance an exponential fashion when the motor temperature rise comes close to the upper working limit of the insulation.
Insulated bearings
Electric motor bearings can decline over time for a number of reasons but the most common reasons that can cause electrical decline or failings are circulating currents and common mode voltages. Circulating currents are often found in all motor. Motors with a bigger frame are more at risk and proposes more risk to damaging the bearings.
Circulating current is usually the result of an imbalance in the motor and the voltage it devises between the rotor and stator. Circulating current can actually pass through the motor bearings as it is the easiest path to flow through. This can result bearing showing signs of frosting or fluting.
Common mode voltage can also cause substantial damage to motor bearings. If using a VFD (Variable Frequency Drive) to drive a motor, it is likely common mode voltage will occur. Unfortunately you cannot eliminate common mode voltage but you can highly reduce the risk of damaging motor bearings. The easiest way to do this is use insulated bearings. Insulated bearings won’t allow stray currents to pass or flow through bearing creating circulating currents.
If using a motor 100Hp (75kw) or more, it is almost certain you should use insulated bearings, the risk is generally very high that circuiting current and common mode voltage will damage motor bearings, ultimately causing damage to the application and the motor itself. Smaller frame motors are still at risk as they can suffer from capacitive discharge current from the rotor. Insulating one or two bearings will help prevent this from happening.
Common practice of insulated bearings is use one at the NDE (non-drive end). This will prevent flow of shaft current and will avoid damage to bearing. Even if your motor isn’t fitted with insulated bearings you still are able to change the non-insulated, to insulated bearings, we highly recommend the use of insulated bearing as it adds more protection to the bearing and motor itself.
IE Motor Efficiency Classifications Explained
What is IE?
IE stands for ‘International Efficiency’ and was introduced as an international standard by The IEC (International Electrotechnical Commision). Did you know around 2/3 of industrial energy consumption comes from machines run by electric motors? In 2008, The IEC set about to introduce a new standard (IEC 60034-30) to globally regulate the efficiency classes and legal requirements based upon the energy efficiency of low voltage, three phase motors. The aim of the new efficiency classifications was to create global standardisation of regulations in order to enable international comparisons and to facilitate the certification of electric motors. It currently has three classes with a fourth class to be introduced as a future development: -
IE1 | Standard Efficiency |
IE2 | High Efficiency |
IE3 | Premium Efficiency |
IE4* | Super Premium Efficiency* |
*Future Development
These standards have been adopted as a European and UK standard. IE4 efficiency currently remains in development at this stage with more news to come in the near future.
Costs & Energy Savings
Questions many people ask about higher efficiency motors are usually centred around cost. Yes, the higher the efficiency the higher the purchase cost. The costs of buying an electric motor are deceptive though. In a single year the cost of energy can be up to 10 times the cost of the motor. Higher efficiency motors will naturally cost more due to the intensive production techniques and additional motor costs. What needs to be taken into consideration is the energy savings cost per operating hours of the motor.
Below you can see a pie chart which demonstrates the running cost of a motor vs the purchase cost.
Running Cost V Purchase Cost
Based on recent studies, If you were to take for example a standard IE2 motor at 8000 operating hours per year, the additional cost is typically paid back in around 7 months, and for an IE3 motor around 10 months. Even at only 2000 operating hours per year, the energy saving repays the capital cost in around 3 years.
Summary
Saving energy and saving money go hand in hand. The initial purchase cost of the unit will be more given the higher the efficiency of the motor, but the cost savings in the long term are there to see. Saving energy is important for the planet we live in, saving money at the same time makes it even sweeter!
How Configuring Your Motor For Use in Star Or Delta
If you are using a 3 Phase motor with an inverter with an input of 230VAC, you will need to ensure the motor is configured with its windings in a Delta arrangement. If you require help in doing this, please use the videos below.
Motor in Star Configuration
If you need guidance in checking which way your motor is currently configured, then please watch our useful tutorial on configuring your 3 phase motor in Star here:
Motor in Delta Configuration
If you need guidance in checking which way your motor is currently configured, then please watch our useful tutorial on configuring your 3 phase motor in Delta here:
Why Buy 3 Phase Motors from ACDC Drives?
We use these motors every day, so if you have any questions, just ask! We all know that in the modern workplace often things are needed as fast as possible. That is where we can help. We can also get engineers out to the site, to carry out surveys, or to install and commission motors on existing or new applications. Call our sales team today by phone on 01905 887 667.