
Fed Up Of Repairing an older DC powered Extruder?
Replace Your DC System With A Far More Efficient AC Extruder System!
New plastic extruders are generally supplied with AC motors and Inverter drives instead of the traditional DC system that were commonly used as recently as 5 years ago.
Why Are AC Motors Used On Extruders?
AC motors require less maintenance and have a better power factor when used with a 3 phase Inverter. It has become common practice in the industry to replace a worn out or older DC Motor and Drive on an existing Extruder with an AC motor and inverter.
Do AC Extruders Have Tachogenerators Built In?
Depending on the application and extruder type, a replacement AC motor can be used without the use of an encoder due to the features the Inverter has built in. Encoders give the added benefit of closed-loop vector control with very accurate speed holding of 0.1%. DC motors come with a Tachogenerator which typically have a speed holding of approximately 1%.
Can ACDC Convert My DC Extruder To AC?
An ACDC customer experienced several failures of his DC motors and costly repairs twice within 6 months. On our second call-out visit, the engineer offered to quote for an AC conversion for his machines. The customer decided to opt for an AC motor replacement with an inverter drive on one of his lines as a proof of concept. One prerequisite for this job was that the motor needed to hold constant torque down to zero speed. To enable this, a forced ventilation fan was installed on the AC motor instead of a standard impeller. This fan unit has a separate power supply, allowing the fan to spin at full rpm all of the time rather than motor speeds, meaning that even when the motor is running at very low RPM, the fan is providing the required airflow to prevent overheating. The install was a success, with a very happy customer, who now runs AC Inverters and Motors on all 6 of his extruder lines.
Please Note: If space for a larger AC motor is a problem we can choose a compact square frame design which will be as small as a DC motor of the same Kw rating.
Would you like to discuss options?
Call 01905 887 667
Replacement Extruder Control Panel
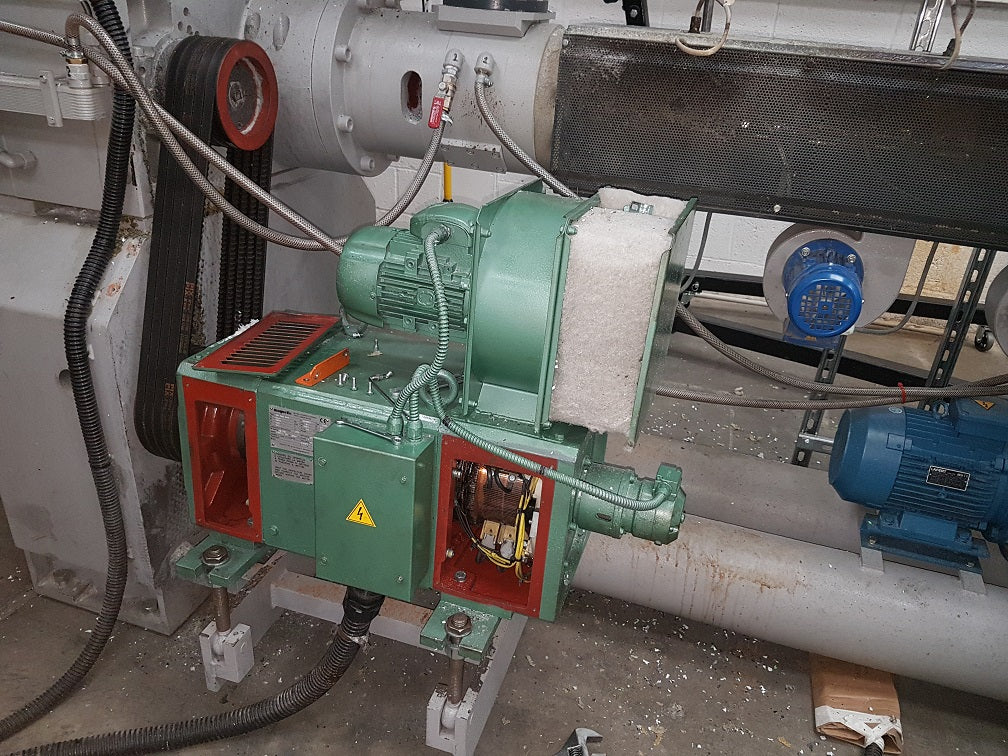
Ageing Panels
Many plastic extruders are 20 to 30 + years old are mechanically sound and work well but have control panels with a DC drive that is showing its age. Some panel control components like the field control are inefficient and crude. In this picture (see Image) the field instead of being controlled with a thyristor bridge has a transformer and external field failure circuit, all components have no easy replacement. In Series with the DC armature circuit is positioned an overload device to give additional overload protection for the DC motor.


Replacement Panel
A modern drive like a Parker SSD (Ex Eurotherm) or Sprint Drive includes these features built in which enable the whole panel to be simplified. This was recently done with a Windmöller & Hölscher DC drive control panel. The Siemens 6RA series DC drive was removed and a Parker SSD drive fitted with many of the features built in enabling the removal of a lot of the electrical switchgear. The improved diagnostic functions reduces machine downtime and increases the reliability. In the new picture electrical shrouding is still required to cover exposed live conductors.
Why not choose AC?
New plastic extruders generally come with AC motors and inverter drives instead of the traditional DC system set up. AC motors require less maintenance and have a better power factor when used with a 3 phase inverter. It is common instead of repairing a DC motor is to have it replaced with a AC motor and inverter. Depending on the application and Extruder type a replacement AC motor can be used without the use of an encoder. Encoders give the added benefit of closed loop vector control with very accurate speed holding of 0.1%.